As mining operations continue, the perimeter dams encircling Rainy River’s Tailings Management Area are raised annually, providing processing capacity for the mine plan and ensuring the safe and responsible storage of tailings within the mine site.
Dam construction consists of a central clay core with downstream filter materials. Clay core is placed in controlled lifts as operators compact each layer to precise quality specifications, maintaining the structural integrity of the dam as they align each new raise with the previous one. As a final step, crews cut the clay to design slope and complete vertical filter lifts made up of sand and gravel with a large filter box around the dam’s 7.5 km perimeter to complete the dam raise at final height.
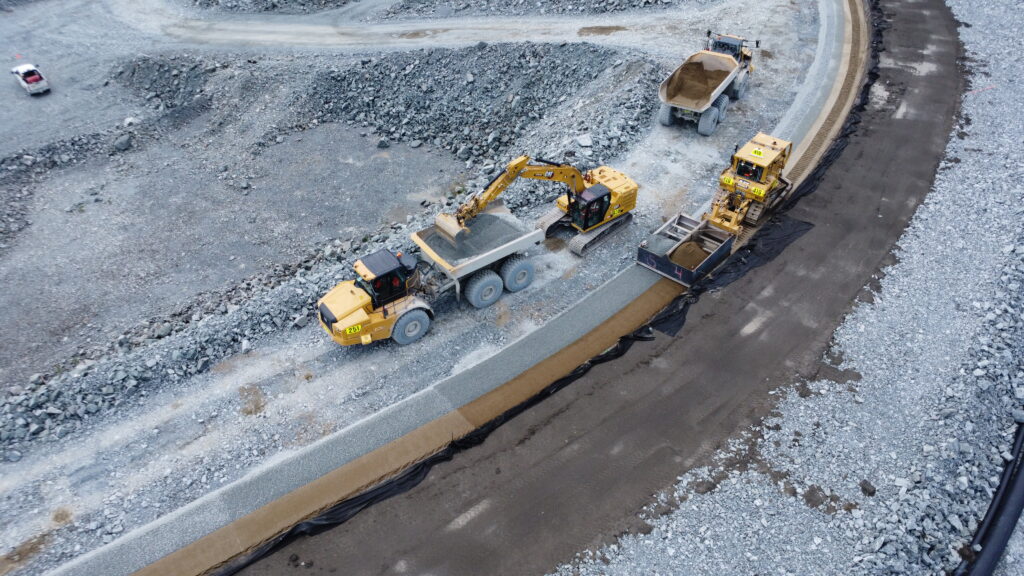
The filter box was originally designed by a site contractor and consists of two bays with a slot on the back for placing the material. Until recently, aligning this finishing lift precisely to core height was a challenge, often requiring re-work to achieve final grade. This inspired New Gold staff to collaborate on an innovative solution to improve both the quality and efficiency of this final step.
“We were throwing around ideas with the construction and maintenance teams on how to make the box functional, easy to use, and safe,” said Travis Hagen, Construction Supervisor. “We used one of our three filter boxes to experiment with, and we met with the welding team to talk about what we were looking for in a finished product.”
The team engineered a filter box with an actuating gate powered by hydraulics. An excavator loads one side of the dual-compartment box with sand and the other with gravel. The loaded box is pulled slowly behind a dozer along the perimeter as a member of the construction team operates the hydraulic gate, releasing a perfectly placed final layer along the dam that requires no re-work.
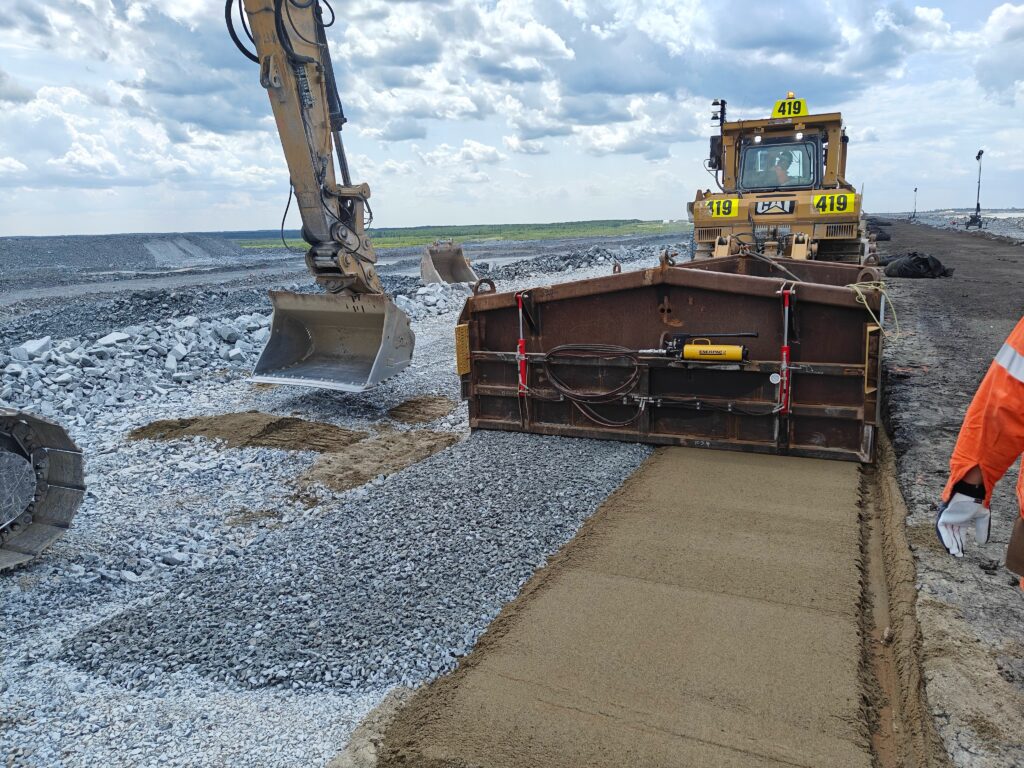
“I thought hydraulic cylinders for adjusting the gate height would be the best fit for safety and productivity,” said Adam Bolen, Maintenance Welding Supervisor at Rainy River Mine. “After the gate was working, we needed a way for the operators to easily adjust it for the desired material height, so we ended up installing scaled rulers with pointers indicating the exact gate height, too.”
After using the new filter box, teams collaborated once more to remove the need for manual hand-pumping of the hydraulic gate.
“Site services had a battery-powered pump that we plumbed into the existing hoses on the box, allowing us to run the hydraulic pump with a battery,” added Travis. “The filters were laid in nice and evenly to grade, labour was minimal, and production increased.”
The post Hydraulic Innovation Puts Finishing Touch on Tailings Dam Construction first appeared on Rainy River Mine.